Cold Storage Capacity Calculation:A Guide to Optimizing Cold Storage Capacity in Food and Beverage Manufacturing
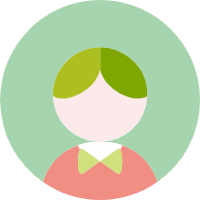
Cold storage is a critical aspect of food and beverage manufacturing, as it ensures the safety and quality of the products throughout the production process. The correct calculation of cold storage capacity is essential for maintaining optimal conditions and preventing product spoilage or damage. This article provides a guide to help manufacturers optimize their cold storage capacity, including factors to consider and steps to take when calculating the necessary space.
Factors to Consider when Calculating Cold Storage Capacity
1. Product types and storage requirements: Different types of products may have different storage requirements, such as temperature, humidity, and air circulation. The cold storage facility should be designed to accommodate these requirements, ensuring the safety and quality of the products.
2. Production volumes: The annual production volume of the company should be taken into consideration when calculating cold storage capacity. Larger production volumes may require larger cold storage facilities to maintain optimal conditions.
3. Storage times: The duration for which products are stored in cold storage should be considered. Products with longer storage times may require larger cold storage facilities to prevent spoilage or damage.
4. Temperature and humidity requirements: Different products may have different temperature and humidity requirements, which should be taken into account when calculating cold storage capacity.
5. Safety and security measures: The cold storage facility should be equipped with necessary safety and security measures, such as fire suppression systems, security cameras, and access controls, to ensure the safety of the products and staff.
Steps to Take when Calculating Cold Storage Capacity
1. Gather information: Collect information on the types of products, production volumes, storage times, and temperature and humidity requirements.
2. Estimate space requirements: Based on the collected information, estimate the required space for cold storage, including the size of the storage rooms, the number of doors and windows, and the necessary equipment, such as refrigerators, freezers, and air circulation systems.
3. Consider the cost: Calculate the estimated cost of the cold storage facility, including land, construction, and equipment costs.
4. Compare costs and benefits: Compare the estimated costs and benefits of different cold storage facilities to determine the most cost-effective solution.
5. Evaluate and adjust: Based on the results of the comparison, evaluate and adjust the cold storage capacity as needed.
Optimizing cold storage capacity in food and beverage manufacturing is essential for maintaining optimal conditions and preventing product spoilage or damage. By considering factors such as product types, production volumes, storage times, and temperature and humidity requirements, manufacturers can ensure that their cold storage facilities are adequately designed and equipped to meet their needs. By following the steps to calculate cold storage capacity and comparing costs and benefits, manufacturers can make informed decisions and invest in the most cost-effective solution for their operations.